The process demands of 21st century ceramics are greater than we have experienced in the past 50 years (yes, I was there and remember it well). Compared to feldspathic PFM restorations, layered lithium disilicate and milled zirconia are even more susceptible to the effects of thermal stress caused by uneven heat patterns.
In order to achieve the best firing results for lithium disilicate and zirconia—as well as any type of layered ceramic—the technician has to accurately control the Ceramic Thermal Conductivity (CTC). Unlike the CTE, the CTC relates to the heat absorption rate of the restorative material as the units are fired to maturation and then cooled down.
It’s critical to keep the vertical and horizontal thermal heat patterns on the firing tray constant. Due to the way conventional muffles are wound, they actually have a hot/cold vertical heat pattern as well as an uneven horizontal heat pattern. Vertically, the temperature drops or rises by approximately 10°C/16°F per 10 mm of height. Therefore, the surface of a 10-mm honeycomb firing tray is going to be 10° hotter than the surface of the furnace platform.
Horizontally, the outer area of the platform fires uniformly but the middle is cooler. For example, the red dots numbered 1, 2, 3 and 4 in the photo below will fire equally but red dot 5 will be 5% cooler. This variable surface temperature makes crown position on the platform especially important when firing multiple single-unit cases in order to achieve a consistent surface finish and shine.
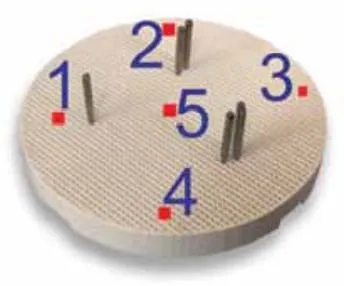
Rapid firing rates exacerbate uneven heat absorption. Also, fast cooling leaves the recrystallization of the porcelain uneven and loaded with stress tension; this can cause a delayed stress crack/fracture, which can occur in 20 minutes or even 20 months.
The Invention
This uneven heating phenomenon is what led to the development of the Wonder Z-Ring. In the early 1990s, my friend Doug Boutell, CDT, and I were experimenting with heat ring materials like kaolin paper and also tried removing the center core of honeycomb material to form a heat ring. At one point, I flashed back to my grandmother explaining to me when I was five years old about why she cooked roast in a Dutch oven rather than a regular pan with low sides. That led to me making a heat ring using high-heat stainless steel strips, and Doug and I were amazed at the depth of color of the fired feldspathic ceramic.
That was the prototype of Wonder Z-Ring (shown here), a honeycomb firing tray with an adjustable radiant heat ring. It keeps the firing zone even vertically and horizontally, allowing the ceramic’s crystal structure to expand equally in both vertical and horizontal dimensions. Because it minimizes the heating up and cooling down problems associated with ceramics, it eliminates dull glaze finishes, increases vitality and helps ensure the long-term structural integrity of the restoration.
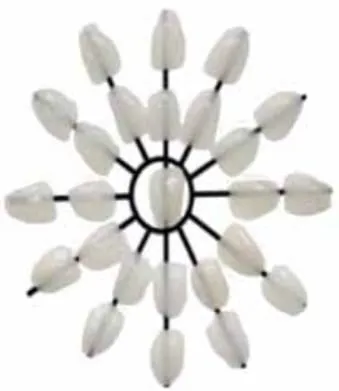
The Wonder Z-Ring also eliminates the variables caused by changes in barometric pressure during firing, which helps control translucency. Without it, a 10% increase in the barometric pressure requires an increase of 2°C to the firing cycle to maintain translucency. For example, the tabs shown below were fired all at one time inside a Wonder Z-Ring. Because of consistent pressure and even heat, there are no perceivable differences in the clarity in any of the tabs. We even measured the percentage of ink density in digital photos of each tab using an optical scanner.
More Ways to Manage the Firing Process
• Use a bonding layer for lithium disilicate and zirconia. With feldspathic PFM restorations, new porcelain layered over fired porcelain fuses to the previously fired layer. However, the layering porcelain for lithium disilicate and Yz don’t fuse to the base core material; instead, they are held on by compression and a slight mechanical lock from surface irregularities. Because of this, the veneering layer is at higher risk of shearing off due to structural fatigue at the interface of the layered porcelain and the pressed or milled frame, a tendency that’s exacerbated by uneven heating and cooling. To enhance bonding, I recommend using a wetting or bonding layer of lower fusing/low viscosity ceramic with the correct CTE—one that is lower than that of the veneering ceramic—to provide a “union zone” between the core material and the veneering ceramic.
• Use the correct entry temperature. Even heating during the drying process affects the translucency and shrinkage of the fired ceramic layers. Doug Boutell and I tested several brands of porcelain ovens, recorded shrinkage and used an SEM/energy-dispersing X-ray analysis to measure H2 O content. We found that the optimum temperature setting for furnace muffle entry for any layered porcelain is between 400°C /752°F to 450°C/842°F. Temperatures higher or lower than that range didn’t remove any more water vapor—which causes steam tears—nor did they improve translucency.
An average drying time of five minutes with 35% to 40% humidity or seven to eight minutes when humidity is over 50% was found to optimize clarity in the ceramic.
For more information on the Wonder-Z Ring, call Dental Creations at 254-772-4661 or visit www.wonderfill.com
Article by: Jim Emmons CDT, FNBC
Jim Emmons, CDT, FNBC, is the developer of products such as the Smart Phone digital analysis system to support his Stella Luminoso Glaze and Bioluminescent shading system, Spectrafire Air Brush System, Wet Palette Humidors, ceramic and porcelain ovens, Life Essence Porcelain System, Biolumé 24k Gold Bonder, Spectrafire Hydro–Vac Plus and Spectrafire Golden Proportion System. A published author and international speaker, he has a training studio in Waco, TX, where he oversees the Spectrafire product line development and distribution. He has recently accepted the position of CEO for Digital Ceramics Sciences LLC.