Vacuum forming and microave-cured resins allowed one lab to refine the denture fabrication process without additional chair time.
WHAT IF A denture fabrication product could offer many clinical benefits without any change in clinical time or technique? (Figure 1)
- Duplicates and maintains border roll clinically established by either functional or compound bordering of the impression.
- Produces a uniform thickness of the base which follows the palatal contours in the final prosthetic.
- Aids in communicating and evaluating expected fit to the patient at the beginning of treatment rather than at the delivery.
- Illustrates outcome and provides an avenue to offer treatment options prior to patient disappointment.
- Provides a final fit for baseplate records. Fewer missed registrations due to looseness of base as undercuts are maintained in baseplate.
- Fewer post-delivery adjustments as comfort issues are addressed at baseplate and try-in stage. Any adjustments made are final as the base becomes part of the completed denture.
In order for us to justify implementing a technique or product to offer, we must establish the benefits for ourselves and our dental professional clients. In 1988, I was introduced to a technique and product offering that eliminated several issues concerning the records and try-in appointments associated with removable prosthetics/dentures, which added no extra chair time.
Vacuum forming and the implementation of microwave-cured resins (NATURE-CRYL® MC, GC America) allowed me to refine the original technique in laboratory labor manufacturing time, uniformity of base thickness, and speed of cure to accommodate daily use and recommendation.
Fabrication Instructions
STEP 01 Box and pour a definitive impression using WonderFormer (Dental Creations) and Coecalâ„¢ Type III Dental Stone (GC America) (Figure 2).
STEP 02 After the stone sets, remove it from former and trim the model to provide a land area and minimal model thickness which does not intrude or destroy vestibular area.
STEP 03 Next, vacuum form .080 sheet of tray/baseplate (Keystone Industries) polystyrene over model. Post forming thickness will present itself between 1.5 to 1.8mm which offers an ideal completed base thickness and rigidity in acrylic. The benefit of vacuum forming rather than waxing is a uniformity of base that follows the contour of the palate (Figure 3).
STEP 04 Trim the forming material to the land area leaving the vestibular molded area intact.
STEP 05 Invest the model in lower the half of a microwave flask covering all but the polystyrene. Once hard, paint land area of investment with COE-SEPTM (GC America) tinfoil substitute and invest upper half of flask (Figure 4).
STEP 06 Once the investment has set, remove the bolts and place the flask vertically in a dedicated microwave oven and irradiate for 1 minute at 500 watts. This creates steam which should release the flask halves (Figure 5a). Remove the polystyrene from the model. If is not soft enough to remove without damaging the model, flame brush the polystyrene with a blazer torch or similar and peel off.
STEP 07 Coat both halves of the flask with COE-SEP similar. Then, dry with warm air to speed up the process.
STEP 08 Mix NATURE-CRYLMC to the correct powder liquid
ratio and allow it to reach recommended pack state (dough-like, not sticky and not snappy.) To avoid waste, I suggest halving the amounts recommended for a standard sized complete denture.
STEP 09 Trial pack mold, trim flash, and if possible, tighten the bolts while the flask is under a pressure of 1500 psi (Figure 5b). This maintains final closure pressure without release. The best compress for the microwave technique is a style that has a plunger press cap. This allows for cinching the nuts unobstructed.
STEP 10 Next, cure vertically for 3 minutes at 500 watts, remove it from oven, and allow it to bench cool for 25 minutes. Submerge it in lukewarm water and then let it cool for an additional 20 minutes.
STEP 11 Deflask, polish and finish base acrylic (Figures 6-7).
STEP 12 Adapt a wax rim following professional standard dimensions. Sticky wax works nicely to fasten wax against acrylic (Figure 8).
STEP 13 Construct the mounting model by blocking out the major undercuts with PVS putty and pouring a stone base. This allows for articulation and easy repeated placement and removal of base from articulator (Figure 9).
STEP 14 Base and rim are sent back for a records appointment and subsequent tooth try-ins (Figure 10).
A technique for waxing and processing on a completed base will be covered in the next article.
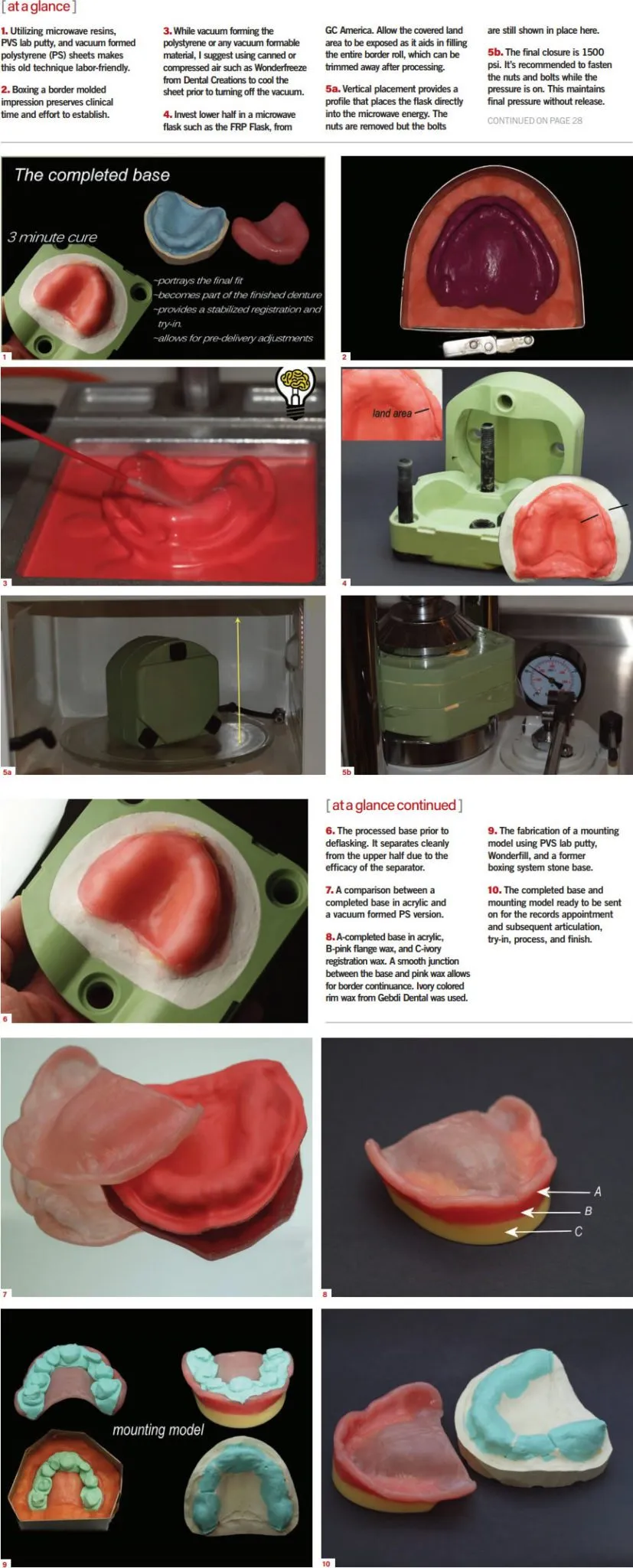
Article by: Tom Zaleske
About the Author: Thomas Zaleske is the owner of Matrix Dental Laboratory in Crown Point, Indiana, and has more than 34 years of experience in removable prosthodontics. He regularly lectures on providing high-quality service to dentists and, most importantly, to their patients. He can be reached at matrixdental@comcast.net and at zaleske.com